honeycomb compression test|ASTM C365 Compression Testing of Sandwich Core : department Store Through the static compression test, the thesis has researched on the performance of static compression on honeycomb paperboard with different thickness and different nest. web1 dia atrás · Feb. 29—MORGANTOWN — John Kelley never hid from controversy. Coaching cliches—the University High football coach rarely used them. If you wanted to venture down the path of knowing what was .
{plog:ftitle_list}
webView the profiles of people named Angel Dos Santos Aveiro. Join Facebook to connect with Angel Dos Santos Aveiro and others you may know. Facebook gives.
ASTM C365 is a test method that determines the compressive strength and modulus of sandwich core specimens. These sandwich constructions can include core materials with continuous bonding surfaces such as balsa wood and .
Permissible core material forms include those with continuous bonding surfaces (such as balsa wood and foams) as well as those with discontinuous bonding surfaces (such .In the compression tests, a circular indenter with diameter of 100.0 mm was utilized to the tensile/compression tester. The test speed of compression loading was set at 1.0 mm/min for composite panel specimens. Figure 2 shows the photo images of the compression test and composite panel specimen. Table 1. Dimensions of honeycomb cores for . Through the static compression test, the thesis has researched on the performance of static compression on honeycomb paperboard with different thickness and different nest.
The flatwise tension-compression test seen in Figure 1 was used to measure the tensile and compressive . Figure 4 , Compression/shear test of honeycomb core Figure 5 , Progression of core deformation during a pure shear test. 396. Figure 6 , Yield surface for C1 core. S is the ratio of shear stress to the shear yield strength. The numerical and test results showed that the manufacturing geometric defects of the cell walls showed little influence on the ultimate flatwise compressive strength. . Qi Z. Experimental and numerical investigation of the effect of entrapped air on the mechanical response of Nomex® honeycomb under flatwise compression. Compos Struct 2017 . The stress-strain response and deformation mechanism of a range of Nomex honeycomb cores tested under in-plane compression has been examined experimentally. The cores with a thin wall displayed ext. pression test and stabilized compression test (for sandwich panels). In the first type, samples have the dimensions of 76.2 × 76.2 × 15.9 mm for aluminum core or 12.7 mm for nonmetallic core.
This page titled 16.2: Compression of a Honeycomb: Experimental is shared under a CC BY-NC-SA 2.0 license and was authored, remixed, and/or curated by Dissemination of IT for the Promotion of Materials Science (DoITPoMS) via source content that was edited to the style and standards of the LibreTexts platform. how to design honeycomb feature https://youtu.be/BSDcmVwuFwQhttps://youtu.be/lSBD3ruZkeY The out-of-plane compression test was performed using a universal testing machine with a loading speed of 2 mm/min. Compression tests in the horizontal direction of wood were performed on the honeycomb structures of A 1, B 1, C 1, D 1, and A 2, B 2, C 2, and D 2. The experiment was divided into eight groups, with five samples in each group.
In-plane compression test of S-shaped reinforced honeycomb cores. To investigate the mechanical properties of S-shaped reinforced honeycomb cores under in-plane compression, quasi-static compression experiments were conducted using an AGS-X electromechanical universal testing machine (Shimadzu Corporation). The compression experiment was carried out on the universal test machine with sandwich structure and the test speed was set as 2 mm/min. The results show that the failure occurs from one end when the aluminum honeycomb faces with flat compression load alone, while the failure of the sandwich structure starts from the middle of the core.Paper Honeycomb – Determination of Compression Strength 9 Expansion The expansion has a serious influence on the compression strength. The compression strength test shall be performed at honeycomb nominal expansion (75%). Form Test piece shall have an isoform shape, at least on pressure area plus two additional cells in each direction. Form 2.6 Lamination strength test of honeycomb. . According to the results of the flatwise-compression test, it was revealed that some factors, including height and angle of the core, the weight .
All specimens were compressed with a constant velocity of 2 mm/min. A 3D digital image correlation (DIC) system was used to record the real-time strain of the composite sandwich cylinders during compression test. Besides, there was a camera behind the specimen to record the whole compression process. Download: Download high-res image (212KB)
technical revisions. Photographs exhibiting revised test methods are shown in Figure 1. Flatwise Tension Flatwise Compression Edgewise Compression Water Migration Honeycomb Node Tensile Strength Figure 1: Recently revised D30.09 . 5.3 In order to prevent local crushing of some honeycomb cores, it is often desirable to stabilize the facing plane surfaces with a suitable material, such as a thin layer of resin or thin facings. Flatwise compressive strength data may be generated using either stabilized specimens (reported as stabilized compression strength) or non-stabilized specimens . In terms of the honeycomb structure, Fig. 17 shows the start and end positions of compression test. Table 8 gives the measured displacements, strains and Poisson’s ratio of honeycomb composite.
Standard Test Method for Flatwise Compressive Properties of
The universal hydraulic test machine YDL-1000 (as shown in Fig. 6, Changchun Machinery Science Research Institute Co., Ltd., the maximum test force is 1000kN) was used for the compression performance test of the honeycomb sandwich structure. Closed-loop displacement control was utilized during the test procedure, maintaining a constant . Buckling stress of honeycombs are predicted based on σf using standard equations and validated with quasi-static compression test along the channels of honeycombs with varying relative densities.
The quasi-static compression test cases for aluminium and Nomex™ honeycomb materials were simulated numerically. Fig. 5 shows the typical stages of the quasi-static compression test on aluminium honeycomb material. Three different regimes can be observed: at low strains a linearly elastic region and buckling, followed by progressive folding .
C363/C363M-24 Standard Test Method for Node Tensile Strength of Honeycomb Core Materials . Structural Test Methods. D7136/D7136M-20 Standard Test Method for Measuring the Damage Resistance of a Fiber-Reinforced Polymer Matrix Composite to a Drop-Weight Impact Event The simulation studies and deformations in the samples following the compression test are shown in (Figure 8(a)–(f)). As can be seen in side-by-side images, the deformations of the samples were similar in the simulation analysis and following the compression test in terms of elastic buckling, plastic buckling and cell wall crush.Title: Mechanical Characterization of Reinforced 3D Printed Honeycombs for Crashworthiness. Highlight: Research is conducted according to an integrated experimental and computational approach to design, fabricate, test, and model structures through finite element analysis for validation and trade-off assessment. - GitHub - veekc/FEA-of-compression-test-of .
The primary compression test procedures were the same under different temperatures, except samples had to be heated in the temperature chamber for 20 mins before the compression program started. . processes, the corresponding stress–strain curves, and energy absorption efficiency curves for quasi-static compression of honeycomb structures . In the test, the test machine exerted stress on the honeycomb structure at a constant crosshead displacement rate of 5 mm/min. The compression was stopped to unload as the honeycomb completely collapsed when the pressures increased too rapidly. Compared with out-of-plane pressures, in-plane pressures of honeycombs are smaller. Figure 6: Schema tic of the honeycomb core shear-compression test fixture defining u and t. 3. RESULTS . Table 2 shows the shear-compression testing results for the studied honeycomb c ore.
The stress-strain relationship on which the current honeycomb material model is based is typically measured using the flatwise-compression specimen depicted in Figure 2. The specimen is based on that detailed in the standard test methods for conducting flatwise compression and tension tests (ASTM C365 [26] and ASTM
Paper Honeycomb Determination of Compression Strength
how to test hardness of material
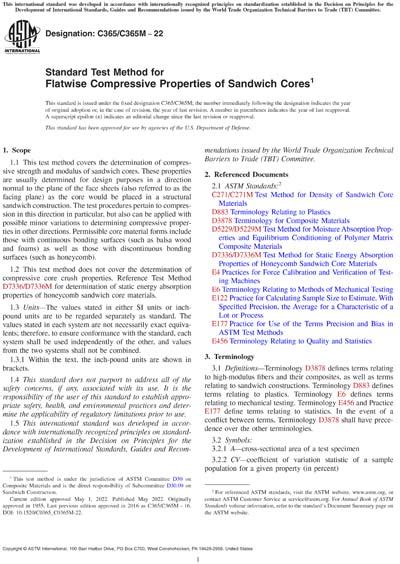
how to test hardness of metal

ASTM C365 Compression Testing of Sandwich Core
Aprovação de álbuns online. Apresente as diagramações em álbuns digitais folheáveis e personalizados, e receba feedbacks dos clientes de forma organizada. Desde que comecei a usar o serviço não tive mais problemas com clientes. Agora eles escolhem as fotos que mais gostaram com muito mais facilidade, e ainda adquirem fotos excedentes.
honeycomb compression test|ASTM C365 Compression Testing of Sandwich Core